Katman Yüksekliği – Basım Teknolojileri – Basım Teknolojileri Ödevleri – Basım Teknolojileri Ödev Ücretleri – Basım Teknolojileri Bölümü
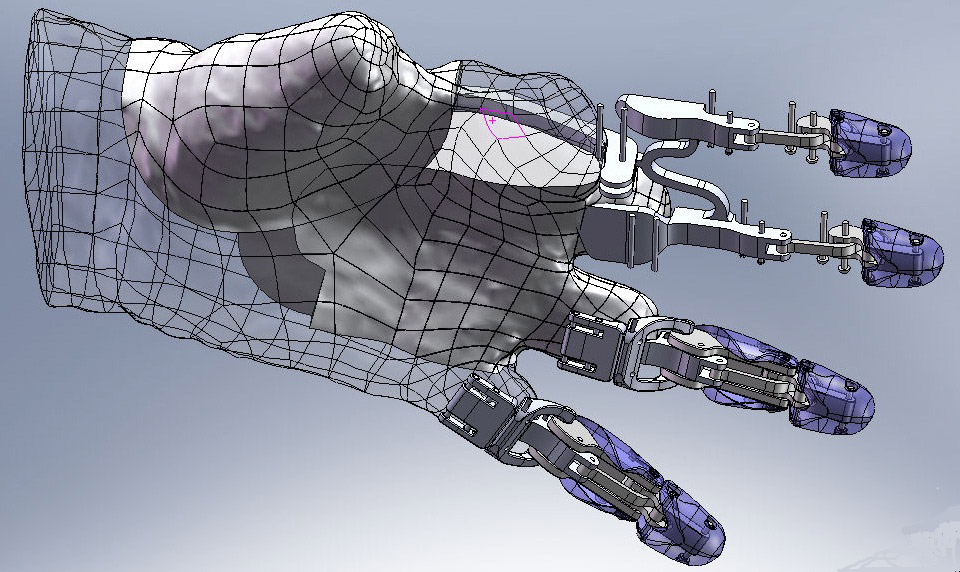
Katman Yüksekliği
Her 3B baskı teknolojisi, her seferinde bir katman olarak üretilen parçalara dayanır. Bir parçanın kalitesine ve yüzey kalitesine katkıda bulunan bir dizi faktör olsa da, her bir katmanın yüksekliği (bazen z ekseni çözünürlüğü olarak da adlandırılır) genellikle etkilenecek en basit parametredir.
En temel düzeyde, bir parça daha küçük bir katman yüksekliğiyle yazdırıldığında, daha pürüzsüz bir yüzeye sahip olacak ve daha yüksek doğrulukta daha ince ayrıntılar üretebilecek, ancak yazdırma süresi artacaktır.
Daha kalın katman yükseklikleri, parçaların daha hızlı yazdırılacağı anlamına gelir, ancak katmanlar yüzeyde görünür görünebilir ve doğruluk o kadar yüksek olmayabilir. İnşa süresi ile katman yüksekliği arasındaki bu ilişki doğrusaldır. Örneğin, 50 mikron katman yüksekliğine sahip bir parça üreten bir baskının, 100 mikron katmana sahip bir parçanın yazdırılması iki kat daha uzun sürecektir.
Çoğu 3B yazıcının varsayılan bir katman yüksekliği vardır ve yalnızca bu varsayılanların dışında parametreler gerektiren özel durumlar vardır (örneğin, çok yüksek ayrıntılı modeller veya çok hızlı oluşturma süreleri). Ortak katman yükseklikleri sunulmuştur.
Bunlar, her bir teknoloji için “yüzey düzgünlüğü” ölçüsü için yararlı bir referans görevi görür; Malzeme Püskürtme en pürüzsüz ve FFF genellikle en pürüzlü finisaja sahiptir.
Çoğu uygulama için, sunulan ortak katman yükseklikleri her teknoloji için yeterli olmalıdır. Bir parçanın tasarımında estetik veya uyum (ör. geçmeli geçmeler veya birbirine kenetlenen parçalar) önemli bir faktörse, yapım süresi ve maliyeti artmasına rağmen daha pürüzsüz bir yüzey elde etmek için katman yüksekliği azaltılabilir.
Görünüşün kritik olmadığı hızlı prototipler için, daha kalın katman yükseklikleri, parçaların daha hızlı (veya daha düşük maliyetle) üretilmesine izin verir, ancak katman çizgileri, sonradan işlenmedikçe görünür olacaktır.
Büzülme ve Eğilme
3D baskı ile ilgili yaygın bir sorun, baskıların bükülmesi ve büzülmesidir. Çekme ve yamulmanın nedeni tipik olarak 2 mekanizma ile ilişkilendirilebilir: sıcaklık ve sertleşme.
Sıcaklık
Kalıntı gerilmeler, parça çekmesi ve bükülmesinin ana nedenidir. Diferansiyel soğuma nedeniyle basılı bir parça içinde artık gerilimler oluşur. Malzeme Ekstrüzyonu (FFF) ve Toz Yatak Füzyonu (SLS ve DMLS/SLM) teknolojileri, parçaları üretmek için yüksek sıcaklıklar kullanır ve ısı kaynaklı bükülmeye veya büzülmeye karşı hassastır.
Baskının bir alanı soğudukça büzülür. Bu büzülme yapı malzemesinin büzülmesine yol açar. Büzülme aynı zamanda çevredeki alanları da çekerek iç gerilimler yaratır. Bu gerilimler yüksekse, parça eğilir veya aşırı durumlarda çatlar.
Kürleme
Fotopolimerler (SLA/DLP ve Malzeme Püskürtme) işlemleri, baskı sırasında yüksek sıcaklıklar gerektirmez (reçinenin ideal bir çalışma sıcaklığına kadar ilk ısıtılması dışında). Bunun yerine, katmanlar sertleşirken parçalarda eğilme ve büzülme meydana gelir.
Kürleme ışık kaynağına maruz kalındığında, her katman katılaşma sırasında büzülür. Bir katman önceden katılaşmış (ön-büzülmüş) bir katmanın üzerine çekildiğinde, iki katman arasında gerilim oluşur. Sonuç, kıvrılmayı başlatan çevredeki katı tabakayı çeken gerilimlerdir.
3D Yazıcı katman yüksekliği
3D Yazıcı ilk katman kalınlığı
3D Yazıcı katmanlar arası boşluk
Bayat filament nasıl anlaşılır
Büzülme ve Eğilmeyi Azaltma
Bir parçayı zararlı bir şekilde etkileyen eğilme veya çekme olasılığını azaltmanın birkaç yolu vardır. Diferansiyel soğutma sorunlarının çoğu, bir parçanın geniş, kalın alanlarının ince unsurlara bağlanmasıyla ilişkilidir. İnce özellikler çok daha hızlı soğuyarak eğrilmelerine neden olur. Bir tasarımcı olarak, bir tasarım üzerinde duvar kalınlıklarının sabit olmasını sağlamak, eğilme olasılığını azaltmaya yardımcı olacaktır.
Çoğu endüstriyel yazıcı tarafından sunulanlar gibi sıcaklık kontrollü bir yapı ortamında parçaların yazdırılması da eğilme veya çekme olasılığını azaltmaya yardımcı olur.
Büyük, düz yüzeyler eğilmeye özellikle yatkındır ve mümkünse tüm 3B baskı teknolojilerinde bunlardan kaçınılmalıdır. Bir tasarım için büyük, düz yüzeyler gerekliyse, birden çok bileşenin montajı düşünülmelidir.
Son olarak, baskının yapı plakasına eğilme riski taşıyan parçalarını sabitlemeye yardımcı olmak için destek önemlidir. Destek malzemesinin nereye yerleştirildiğini ve ne kadar kullanıldığını anlamak, bir baskının sonucunu iyileştirmeye yardımcı olacaktır. Bu özellikle SLA/DLP ve DMLS/SLM için önemlidir.
3D baskılı parçalar, katman katman eklenerek oluşturulur. Spesifik 3B baskı teknolojisine ve 3B modelin karmaşıklığına bağlı olarak bu, her katman üzerine inşa edilecek bir platform gerektirdiğinden, 3B baskının destek yapıları gerektirdiği anlamına gelebilir. Çoğu teknoloji için, bir modelin başarılı ve doğru bir şekilde basılabilmesini sağlamak için destek gereklidir.
Hangi teknolojinin kullanılacağına karar verirken, destek yapılarını ve bunların nihai sonucu nasıl etkileyebileceğini dikkate almak önemlidir. Çoğu destek yapısı, çıkarılmaları için son işlem gerektirdiklerinden, yüzey kalitesi üzerinde olumsuz bir etkiye sahip olacaktır.
Bu, lekelere veya yüzey pürüzlülüğüne neden olur. Bölüm 1’de tartışıldığı gibi, FFF ve Material Jetting gibi bazı teknolojiler çözülebilir destek sunarak sökmeyi çok daha kolaylaştırır. Toz veya kum bazlı teknolojiler, metale baskı yapmadıkça destek malzemesi gerektirmez.
Destek genellikle bir modelin altına yerleştirilir ve bu da üstün bir yüzey kaplamasına sahip yukarı bakan yüzeylerle sonuçlanır. Bir modelin estetiği veya uyumu önemliyse, modeli en kritik yüzeyleri yukarı bakacak şekilde yönlendirmek en iyisidir (SLS baskı hariç).
Dolgular
Dolgular (bazen yarıçap olarak adlandırılır), parça tasarımında yer alan yaygın bir özelliktir. Filetolar, köşelerde ve kenarlarda stres konsantrasyonlarını azaltmaya yardımcı olur ve parçaların 3D baskısını kolaylaştırır. Filetolar, yapı plakasından parçaların çıkarılmasına da yardımcı olabilir (özellikle FFF aracılığıyla üretilen parçalar).
Çoğu teknoloji, tüm kenarlarda ve köşelerde “doğal bir fileto” üretir. Örneğin, FFF meme yarıçapına eşit bir dış yarıçap üretirken, SLS parçaları tipik olarak tüm keskin kenarlarda yaklaşık 0,4 mm’lik bir yarıçapa (lazer nokta boyutu) sahip olacaktır.
Filetolar, mümkün olan her yerde 3D baskılı parçaların tasarımına dahil edilmelidir. Minimum 2 mm yarıçap iyi bir başlangıç noktasıdır. Yapı plakasına eklenmiş dış kenarlar için, şekilde gösterildiği gibi herhangi bir destek malzemesi gerektirmediğinden, dolgu yerine 45°’lik bir pah genellikle daha iyi bir çözümdür.
3D Yazıcı ilk katman kalınlığı 3D Yazıcı katman yüksekliği 3D Yazıcı katmanlar arası boşluk Bayat filament nasıl anlaşılır
Son yorumlar