Malzeme İşleme – Basım Teknolojileri – Basım Teknolojileri Ödevleri – Basım Teknolojileri Ödev Ücretleri – Basım Teknolojileri Bölümü
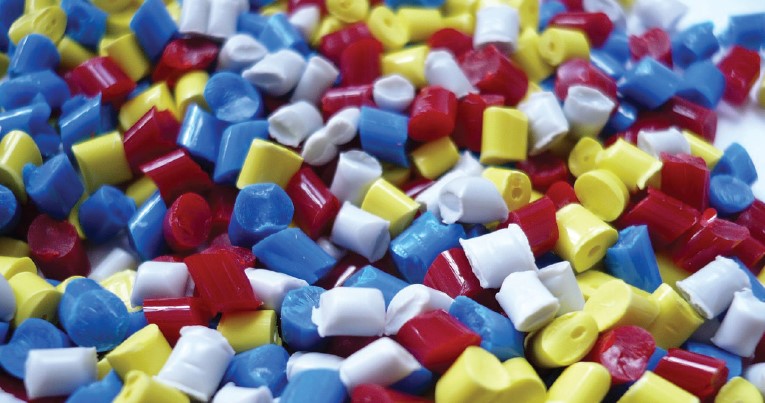
Malzeme İşleme
Belirtildiği gibi, genel tabaka laminasyon kategorisi altında birkaç işlem türü belirgindir. Termal yapıştırma ve sac metal kenetleme bu bölümde ele alınmaktadır. Bir sonraki bölümde, ultrasonik konsolidasyon işlemi için daha derinlemesine bir kapsam sağlanmaktadır.
Termal Yapıştırma
Dünyanın dört bir yanındaki birçok kuruluş, fonksiyonel metal parçaların ve takımların sac laminasyonuna termal yapıştırmayı başarıyla uygulamıştır. Bu yaklaşımın esnekliğini göstermek için birkaç örnekten bahsedilecektir. Daha sonra difüzyonla birleştirilen önceden kesilmiş 1 mm kalınlığında çelik levhalar kullanarak 3D metalik parçaları başarıyla ürettiniz.
Herhangi bir fiziksel süreksizlik olmaksızın tabaka arayüzleri boyunca tane yapısında süreklilik gösterdiler. 0,1 mm kalınlığında düşük erime noktalı Al 4343 (toplam sac kalınlığı 2,5 mm) ile kaplanmış Al 3003 levhaları kullanarak karmaşık soğutma kanallarına sahip alüminyum enjeksiyon kalıplama kalıpları üretti.
Levhalar, yaklaşık, büyük boyutlu bir enine kesitte lazerle kesildi, mekanik bağlantı elemanları kullanılarak birleştirildi, düzeneğin Al 4343 kaplama malzemesinin erime noktasının hemen üzerindeki bir nitrojen atmosferinde ısıtılmasıyla birbirine bağlandı ve ardından öngörülen parça boyutlarına göre işlendi ve tamamlandı.
Ayrıca, sert lehimleme ve lazer nokta kaynak işlemleri kullanılarak tatmin edici katman bağlaması da göstermiştir. Üst ve alt yüzeyleri düşük erime noktalı bir alaşımla kaplanmış daha ince çelik saclardan (0,2 mm kalınlık) benzer bir işlem kullanılarak üretilen metal parçalardır.
Lazerle kesilmiş çelik sacların lehimlenmesiyle uyumlu soğutma kanallarına sahip lamine çelik takımlar üretildi. Benzer şekilde, 0,5 mm kalınlığında çelik saclar kullanılarak otomobil gövde imalatı için kalıplar üretilmiştir. Bunların her biri ve diğer araştırmacılar, metal levhaları termal olarak birleştirmenin, özellikle iç boşlukları ve/veya soğutma kanalları olan karmaşık metal parçalar ve aletler oluşturmak için etkili bir yöntem olduğunu göstermiştir.
Kapsamlı bir şekilde çalışılmasına rağmen, sac metal laminasyon yaklaşımları ticari olarak çok az ilgi görmüştür. Bunun başlıca nedeni, bağla-sonra-şekillendirme işlemlerinin, destek malzemelerini çıkarmak için kapsamlı bir son işlem gerektirmesi ve oluştur-sonra-bağla işlemlerini gelişigüzel, karmaşık geometriler için otomatikleştirmenin zor olmasıdır.
Oluştur-sonra-birleştir süreçlerinde, özellikle bir enine kesitin geometrisi kalan geometriden ayrıysa, laminatların doğru bir şekilde hizalanması zordur ve parçaya özel bir çözüm gerektirebilir.
Bu nedenle, her enine kesitin geometrisinin bitişik olarak birbirine bağlı olduğu yukarı bakan özellikler, kullanımı en kolay olanlardır. Levha laminasyona yönelik ticari ilgi, öncelikle, dahili, konformal soğutma kanallarının geleneksel soğutma stratejilerine göre önemli faydalar sağlayabildiği ucuz, tam renkli kağıt parçalar ve büyük aletler alanındadır.
Malzeme seçimi ve Uygulamaları PDF
Malzeme ve Tasarım PDF
Talaşlı imalat formülleri
Malzeme seçimi Ders Notları
Talaşlı imalat PDF
Tasarımda malzeme seçimi
Malzeme seçiminde dikkat edilecek hususlar
Malzeme seçimi örnekleri
Levha laminasyonunu diğer AM biçimleriyle (kiriş biriktirme, ekstrüzyon ve çıkarma işleme dahil) birleştiren başka bir süreç, Shape Deposition Manufacturing (SDM) idi. SDM ile parçanın geometrisi düzlemsel olmayan bölümlere ayrılır.
Her parça, aşırı boyutlu, ağa yakın şekil bölgesi olarak biriktirilir ve ardından makineyle tamamlanır. Segmentlerin (düzlemsel katmanlar yerine) sıralı biriktirilmesi ve işlenmesi parçayı oluşturur. Doğruluk, malzeme, geometrik özellikler ve fonksiyonel gereksinimler gibi faktörlere bağlı olarak her bir segmentin nasıl üretileceğine karar verilir.
İkincil destek malzemeleri, karmaşık geometrinin yapılabilmesi ve imalattan sonra diferansiyel hareket gerektiren mekanizmalar arasındaki açıklık için yaygın olarak kullanıldı.
Bununla birlikte, gelişigüzel geometriler için tamamen otomatik bir alt bölümleme rutini hiçbir zaman geliştirilmemiştir ve birçok geometri türü için bir insan “uzmanın” müdahalesi gerekmektedir. Sonuç olarak, bazı karmaşık çok malzemeli yapılar için ilginç ve yararlı olsa da, böyle bir sistem hiçbir zaman ticari olarak tanıtılmadı.
Sert Metaller
Sert metal laminatların basit şekiller halinde birleştirilmesi durumunda, bir yapışkan veya termal birleştirme yöntemi kullanmak yerine levhaları cıvatalar ve/veya bir kenetleme mekanizması kullanarak basit bir şekilde birbirine kenetlemek avantajlı olabilir. Sıkıştırma hızlı ve ucuzdur ve belirli bir laminatın kesitini değiştirmek ve/veya malzemelerin kolay geri dönüştürülmesi için laminatların demonte edilmesini sağlar. Ek olarak, kenetleme veya cıvatalama mekanizması, her bir laminatı birbirine göre ayarlamak için bir referans noktası görevi görebilir.
Sıkıştırırken, bir profili bir laminatın bir kenarına basitçe kesmek ve dikdörtgen levhanın üç kenarını kesilmeden bırakmak genellikle avantajlıdır. Böyle bir “profilli kenar laminat” yapısının bir örneği gösterilmektedir. Tabii ki, bu tip profilli kenar aynı zamanda yapışkan ve termal olarak birleştirilmiş katmanlarla da kullanılabilir.
Bu yaklaşımın en büyük yararı, katmanların kenetlenme kolaylığıdır (yani, sağ kenarda görünen açık delikler kullanılarak yapılabileceği gibi, bir dizi delikten laminatların birbirine cıvatalanması).
Bir profil yaklaşımının dezavantajları, çoğu araç için kenetleme kuvvetlerinin laminat arayüzüne dik olması ve laminatların belirli koşullar altında, örneğin basınçlı polimerlerin bir kalıba enjekte edilmesi gibi, birbirinden ayrılabilmesidir (boşluklar bırakarak). böyle bir araçtan yapılmıştır.
Ultrasonik Eklemeli İmalat
Ultrasonik Konsolidasyon (UC) olarak da bilinen Ultrasonik Eklemeli Üretim (UAM), ultrasonik metal dikiş kaynağı ile CNC frezelemeyi birleştiren ve 2000 yılında ABD tarafından ticarileştirilen ve daha sonra Fabrisonics’e lisanslanan hibrit bir sac laminasyon işlemidir.
UAM’de nesne, oda sıcaklığından yaklaşık 200 C’ye kadar değişen sıcaklıklarda, ısıtılmış bir plaka üzerine cıvatalanmış sağlam bir şekilde tutulan bir taban plakası üzerine inşa edilmiştir. Parçalar aşağıdan yukarıya inşa edilir ve her katman, yan yana yerleştirilmiş birkaç metal folyodan oluşur ve ardından CNC frezeleme kullanılarak kırpılır.
UAM sırasında, dönen bir sonotrot, ince bir metal folyonun (tipik olarak 100–150 μm kalınlığında) uzunluğu boyunca hareket eder. Folyo, şematik olarak gösterildiği gibi dönen sonotrode yoluyla normal bir kuvvet uygulanarak taban plakası veya önceki katman ile yakın temas halinde tutulur.
Sonotrode, sabit bir 20 kHz frekansta ve kullanıcı tarafından ayarlanan salınım genliğinde hareket yönüne çapraz olarak salınır. Bir folyo yerleştirildikten sonra, yanına başka bir folyo yerleştirilir. Bu prosedür, tam bir katman yerleştirilene kadar tekrarlanır.
Bir sonraki katman, aynı prosedür kullanılarak daha önce bırakılan katmana yapıştırılır. UAM’de tipik olarak dört katmanlı birikmiş metal folyo bir seviye olarak adlandırılır. Bir seviyenin biriktirilmesinden sonra, CNC freze kafası, bırakılan folyoları/katmanları dilim konturlarına göre şekillendirir (konturun dikey olması gerekmez, ancak yerel parça geometrisine bağlı olarak eğimli veya açılı bir yüzey olabilir).
Bu toplama-çıkarma işlemi, parçanın nihai geometrisi elde edilene kadar devam eder. Bu nedenle, UAM, kullanıcı tarafından seçilen ayarlara bağlı olarak her katmandan sonra veya birkaç katmandan sonra şekillendirmenin meydana gelebildiği bir bağla-sonra-biçim sürecidir. Ek olarak, levha laminasyon işlemlerinde tipik olarak uygulandığı gibi, her tabaka tipik olarak tek bir büyük levha yerine yan yana yerleştirilmiş folyoların bir kombinasyonu olarak biriktirilir.
Malzeme seçimi Ders Notları Malzeme seçimi örnekleri Malzeme seçimi ve Uygulamaları PDF Malzeme seçiminde dikkat edilecek hususlar Malzeme ve Tasarım PDF Talaşlı imalat formülleri Talaşlı imalat PDF Tasarımda malzeme seçimi
Son yorumlar