Malzeme İşleme Temelleri – Basım Teknolojileri – Basım Teknolojileri Ödevleri – Basım Teknolojileri Ödev Ücretleri – Basım Teknolojileri Bölümü
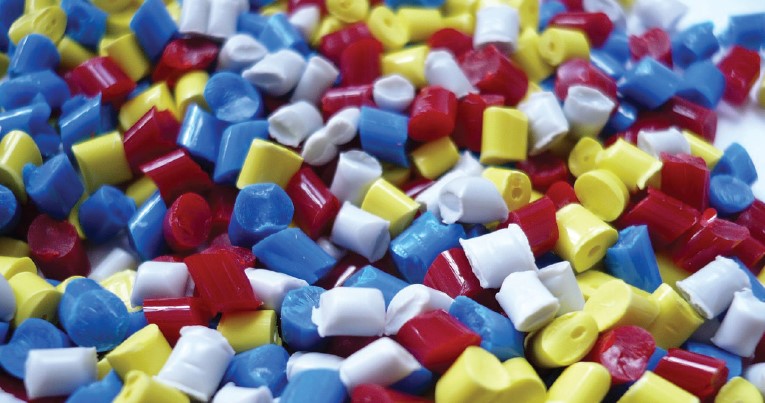
Çözelti ve Dispersiyon Bazlı Biriktirme
Sıcak eriyik biriktirme, basılı olanın malzeme özellikleri için çok özel gereksinimlere sahip olduğundan, mevcut birçok uygulama çözelti veya dispersiyon bazlı biriktirmeye yönelmiştir. Bu, başarılı bir şekilde basılacak kadar düşük viskoziteye sahip bir taşıyıcı sıvı içinde katıların veya yüksek moleküler ağırlıklı polimerlerin verilmesine izin verir. Bu stratejinin kullanıldığı bir dizi polimerik uygulamanın gözden geçirilmesi sağlandı.
Bazı araştırmacılar, polimer ışık yayan ekranlar, elektronik bileşenler ve yüzey kaplamaları ve maskeler gibi orta ölçekli uygulamalar için çok küçük miktarlarda polimerin ince katmanlar halinde doğru bir şekilde biriktirilmesinde çözelti ve dispersiyon tekniklerini kullanmışlardır.
Örneğin, iletken polimerlerin mürekkep püskürtmeli birikimini kullanarak ışık yayan polimer diyot ekranları geliştirmek için bir teknik sunun. Üç farklı elektrominesans polimer (poliflorin ve iki türev), ağırlıkça %1-2 oranında organik çözücüler içinde basılmıştır.
Başka bir örnek olarak, polimer ışık yayan ekranların yaratılmasıyla ilgili bir dizi başka sonucu bildirin: bir poli(p-fenilen vinilen) (PPV) öncüsü, ağırlıkça %0,3’lük bir çözelti olarak basıldı; ve PPV türevleri, tetralin, anizol ve o-ksilen gibi çözücüler içinde ağırlıkça %0.5-2.0 çözeltilerde basılmıştır. Bu tür düşük ağırlık yüzdeleri tipiktir.
Seramiklerin biriktirilmesinde, düşük viskoziteli bir taşıyıcının kullanılması da popüler bir yaklaşımdır. Örneğin, dağıtıcı, bağlayıcı ve plastikleştirici katkı maddeleri ile endüstriyel metillenmiş ispirto içinde dağıtılan kullanılmış seramik tozu, hacimce %4,5 zirkonya olan bir malzemeyle sonuçlandı.
Ortaya çıkan malzemenin 20°C’de 3.0 cP viskozitesi ve 1.000 s 1 kesme hızı vardı. Zhao ve ark. [29], oktan ve izopropil alkolde taşınan çeşitli zirkonya ve mum kombinasyonlarını, sedimantasyonu azaltmak için bir dağıtıcı eklenmiş olarak test ettiler. Bu malzemelerin viskoziteleri 25°C’de 0.6-2.9 cP idi; son olarak seçilen, hacimce %14.2 zirkon idi.
Bununla birlikte, bu özel uygulamalar için çözelti ve dispersiyon biriktirme başarısına rağmen, özellikle karmaşık, büyük, 3B bileşenlerin inşa edilmesi potansiyeli göz önüne alındığında bazı ciddi dezavantajlar vardır.
Çözeltilerde ve dispersiyonlarda kullanılan düşük polimer ve katı konsantrasyonları, biriktirilebilecek toplam malzeme miktarını kısıtlayacaktır. Ek olarak, damlacığın etki alanı içinde bu malzemenin birikme modelini kontrol etmek zor olabilir.
Diğerlerinin yanı sıra, damlacığın kenarı çevresinde biriken malzeme halkalarının oluştuğunu bildirin. Bunu, kurutma damlasının temas hattının alt tabakaya sabitlenmiş olmasına bağlamaktadırlar. Sıvı kenarlardan buharlaşırken, çözünenleri kenara taşıyarak içten tekrar doldurulur. Bu etkinin damlacık kurutma koşullarının kontrolü ile hafifletilebileceğini iddia etmektedirler.
Çözeltiler veya dispersiyonlarla, özellikle uçucu çözücülere dayalı olanlarla ilgili diğer bir zorluk, bu malzemelerin kullanımının çok kısa bir süre sonra memede çökeltiler oluşmasına neden olabilmesidir, bu da memeyi tıkayabilir ve çökelmeyi güvenilmez veya imkansız hale getirebilir.
Malzeme seçimi ve Uygulamaları PDF
Malzeme ve Tasarım PDF
Talaşlı imalat formülleri
Talaşlı İmalat Yöntemleri Ders Notları
Talaşlı imalat PDF
Malzeme seçimi Ders Notları
Tasarımda malzeme seçimi
Malzeme seçiminde dikkat edilecek hususlar
Malzeme İşleme Temelleri
Önceki bölümde tartışılan endüstri ve araştırma uygulamalarının kanıtladığı gibi, malzeme püskürtme, başarılı bir AM teknolojisi olma açısından halihazırda güçlü bir dayanağa sahiptir. Bununla birlikte, gelişiminin daha fazla büyümesini engelleyen bazı ciddi teknik eksiklikler var.
Bu sorunları belirlemek ve ele almak için, geliştiricileri tarafından alınan ilgili olgular ve stratejik yaklaşımlar anlaşılmalıdır. Sonraki iki bölümde, baskı işleminin teknik zorlukları ana hatlarıyla belirtilmiş, fonksiyonel polimerlerin biriktirilmesiyle ilgili sınırlamalarının en önemlileri tanımlanmış ve bu sınırlamaların şu anda nasıl ele alındığı özetlenmiştir.
Üç boyutlu imalat için püskürtme, baştan sona zorlu teknik sorunlar içeren son derece karmaşık bir süreçtir. Bu zorluklardan ilki, sıvı malzemenin formülasyonudur.
Malzeme başlangıçta sıvı formda değilse, bu, parçacıkların bir taşıyıcı sıvı içinde süspanse edilmesi, malzemelerin bir çözücü içinde çözülmesi, katı bir polimerin eritilmesi veya bir monomer veya prepolimer formülasyonunun bir polimerizasyon başlatıcı ile karıştırılması anlamına gelebilir. Çoğu durumda, kabul edilebilir özellikler elde etmek için sıvıya yüzey aktif maddeler gibi başka maddeler eklenir.
Tüm endüstriler, iki boyutlu baskı için mürekkep karışımına ayrılmıştır ve gelecekte bunun üç boyutlu imalat için de geçerli olacağını varsaymak mantıklıdır.
Aşılması gereken ikinci engel damlacık oluşumudur. Mürekkep püskürtmeli biriktirme yöntemlerini kullanmak için, malzemenin sürekli bir sıvı hacminden çok sayıda küçük ayrı damlacıklara dönüştürülmesi gerekir.
Bu işlev genellikle yazdırılan malzeme, ilgili donanım ve işlem parametreleri arasındaki ince ayarlı ilişkiye bağlıdır; damlacık oluşumunu sağlamanın bir dizi yöntemi bu bölümde tartışılmaktadır. Küçük parçacıkların eklenmesi gibi malzemede yapılan küçük değişiklikler, fiziksel kurulumdaki değişiklikler gibi damlacık oluşturma davranışını da önemli ölçüde değiştirebilir.
Üçüncü bir zorluk, bu damlacıkların birikmesinin kontrolüdür; bu, damlacık uçuş yolu, çarpma ve alt tabakanın ıslanması veya etkileşimi sorunlarını içerir. Baskı işlemlerinde, baskı kafası veya alt tabaka genellikle hareket eder, bu nedenle damlacıkların yörüngesinin hesaplanmasında bu husus dikkate alınmalıdır.
Damlacıkların varış yerine ek olarak, damlacık hızı ve boyutu da biriktirme özelliklerini etkiler ve meme tasarımı ve çalışması yoluyla ölçülmeli ve kontrol edilmelidir.
Etkilenen damlacığın kalitesi de kontrol edilmelidir: eğer uydu adı verilen daha küçük damlacıklar uçuş sırasında ana damlacıktan koparsa, o zaman biriken malzeme amaçlanandan daha geniş bir alana yayılacak ve birikimin iyi tanımlanmış sınırları olmayacaktır. . Aynı şekilde, damlacık çarpma anında sıçrayarak “taç” denilen şeyi oluşturursa, benzer sonuçlar ortaya çıkar. Tüm etkiler, yazdırılan malzemenin baskı kalitesini olumsuz yönde etkileyecektir.
Aynı zamanda, sıvı malzeme damlacıklarının katı geometriye dönüşümü dikkatle kontrol edilmelidir; tartışıldığı gibi, malzeme püskürtme, basılı malzemenin bir faz değişimine dayanır.
Mevcut baskı teknolojilerinde kullanılan faz değiştirme modlarının örnekleri şunlardır: erimiş bir malzemenin katılaşması (örn. mum, lehim), bir çözeltinin sıvı kısmının buharlaşması (örn. bazı seramik yaklaşımlar) ve bir fotopolimerin kürlenmesi (örn. Objet , ProJet makineleri) veya diğer kimyasal reaksiyonlar vb.
Faz değişimi, damlacık uçuşu sırasında veya çarpmadan hemen sonra meydana gelmelidir; Bu dönüşümün zamanı ve yeri, damlacığın alt-tabaka ile etkileşimini ve yaratılan nihai birikimi de etkileyecektir. Konuyu daha da karmaşık hale getirmek için, damlalar düzensiz bir şekilde katılaşarak çarpıklık ve diğer istenmeyen sonuçlar yaratabilir.
Malzeme seçimi Ders Notları Malzeme seçimi ve Uygulamaları PDF Malzeme seçiminde dikkat edilecek hususlar Malzeme ve Tasarım PDF Talaşlı imalat formülleri Talaşlı imalat PDF Talaşlı İmalat Yöntemleri Ders Notları Tasarımda malzeme seçimi
Son yorumlar