Özellik Geliştirme – Basım Teknolojileri – Basım Teknolojileri Ödevleri – Basım Teknolojileri Ödev Ücretleri – Basım Teknolojileri Bölümü
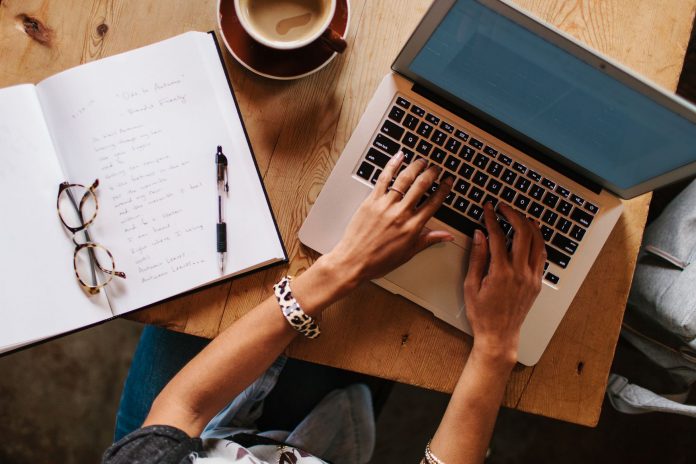
Termal Olmayan Teknikler Kullanarak Özellik Geliştirmeleri
Toz bazlı ve ekstrüzyon bazlı işlemler genellikle gözenekli yapılar oluşturur. Çoğu durumda, bu gözenekliliğe siyanoakrilat gibi daha yüksek mukavemetli bir malzeme sızabilir.
Sızıntılar ve çeşitli türlerde nano-kompozit takviyeler kullanılarak AM parçalarının mukavemetini, sünekliğini, ısı sapmasını, tutuşabilirlik direncini, EMI korumasını veya diğer özelliklerini artırmak için tescilli yöntemler ve malzemeler de geliştirilmiştir.
Fotopolimer malzemeler için yaygın bir son işlem işlemi sertleştirmedir. İşleme sırasında, birçok fotopolimer tam polimerizasyona ulaşamaz.
Sonuç olarak, bu parçalar, parçanın yüzeyini ve yüzey altı bölgelerini tamamen iyileştirmek için parçayı UV ve görünür radyasyonla dolduran bir cihaz olan Post-Cure Aparatına konur. Ek olarak, parça, fotopolimerin tamamen kürlenmesine yardımcı olabilecek ve bazı durumlarda parçanın mekanik özelliklerini büyük ölçüde geliştirebilecek şekilde, düşük sıcaklıktaki bir fırında ısıl kürlenmeye tabi tutulabilir.
Termal Teknikleri Kullanarak Özellik İyileştirmeleri
AM işleminden sonra birçok parça, özelliklerini geliştirmek için termal olarak işlenir. Metaller için DED ve PBF teknikleri söz konusu olduğunda, bu ısıl işlem öncelikle istenen mikro yapıları oluşturmak ve/veya artık gerilimleri azaltmak için ısıl işlemdir.
Bu durumlarda, kullanılan belirli metal alaşımı için geliştirilen geleneksel ısıl işlem tarifleri sıklıkla kullanılır. Bununla birlikte, bazı durumlarda, AM parçası içindeki ince taneli mikro yapıyı korurken, gerilimi azaltma ve sünekliği artırmaya devam etmek için özel ısıl işlem yöntemleri geliştirilmiştir.
Metalleri ve seramikleri doğrudan işleyebilen DED ve PBF tekniklerinin ortaya çıkmasından önce, AM kullanarak metal ve seramik yeşil parçalar oluşturmak için birçok teknik geliştirildi. Bunlar daha sonra yoğun, kullanılabilir metal ve seramik parçalar elde etmek için fırında sonradan işlendi. Bağlayıcı püskürtme, bu amaçlar için yaygın olarak kullanılan tek AM işlemidir.
Ham parçaların fırında işlenmesine yönelik temel yaklaşım gösterildi. Ham bir parçayı fırın işlemeye hazırlamak için tipik olarak birkaç hazırlık aşaması yapılır. Fırın sızması için LaserForm ST-100’den yapılmış metal bir yeşil parçanın hazırlanması adımlarını gösterir.
Fırın ayırma, sinterleme ve sızmadan sonra bir ExOne bağlayıcı püskürtme işleminden yapılan bir enjeksiyon kalıplama aracını gösterir. Bir enjeksiyon kalıbında yüzey konturlarını takip eden soğutma kanallarının (konformal soğutma kanalları) kullanılmasının önemli ölçüde kanıtlanmıştır.
Soğutma süresini ve parça bozulmasını azaltarak enjeksiyon kalıbı takımının üretkenliğini artırın. Bu nedenle, uyumlu soğutma kanallarının uygun kullanımı, birçok şirketin üretkenliklerini artırmak için AM tarafından üretilen araçları kullanmasını sağlar.
Fırın işleme sırasında büzülmenin ve boyutsal doğruluğun kontrolü, optimize edilmesi gereken işlem parametrelerinin sayısı ve dahil olan çok sayıda adım nedeniyle karmaşıktır. Bu tip fırın işleme için optimizasyonun karmaşık doğasını gösterir.
tümleşik geliştirme ortamları (ide) amaçları
IDE örnekleri
Ide Nedir
IDE açılımı
What is IDE
İde nedir programlama
ide nedir, ne işe yarar
Yazılım geliştirme Ortamı Nedir
Y ekseni, (F1–F2)/F1, paslanmaz çelik (RapidSteel 2.0) parçaların bronz kullanılarak sızmasının son fırın aşaması sırasındaki boyut değişikliklerini temsil eder. F1, kahverengi kısmın infiltrasyondan önceki boyutu ve F2, infiltrasyondan sonraki boyutudur.
Veriler, 0,3 ila 3,0 inç arasında değişen hem dahili (kanal benzeri) hem de harici (nervür benzeri) özellikler genelinde binlerce ölçümü temsil eder. Birçok faktör üzerinde çalışılmasına rağmen, sızma adımı için yalnızca ikisinin istatistiksel olarak anlamlı olduğu bulundu, atmosferik basınç fırın ve infiltrant miktarı da önemlidir.
Atmosfer basıncı 10 ila 800 Torr arasında değişiyordu. Kullanılan infiltrant miktarı, %85 gibi düşük bir değerden %110 gibi yüksek bir değere kadar değişmekteydi; burada yüzde miktarı, ağırlık ve ölçümlere dayalı olarak parçadaki tüm gözenekleri tamamen doldurmak için gereken teorik malzeme miktarına dayanıyordu.
En düşük toplam büzülmeye sahip faktör kombinasyonlarının, en düşük büzülme değişimine sahip faktörler olmadığı görülebilir. A faktör kombinasyonu en düşük ortalama büzülmeye sahipken, E faktör kombinasyonu en düşük büzülme değişimine sahipti.
Ortalama büzülme bir ölçekleme faktörü kullanılarak kolayca telafi edilebildiğinden, en yüksek doğruluk ve kesinlik için optimum faktör kombinasyonu E faktör kombinasyonu olacaktır.
Tartışılan doğruluk stratejisi izlenirse, benzer bir yaklaşım kullanılarak tüm süreç için (AM kullanılarak yeşil parça üretimi artı sinterleme ve sızma) büzülme varyasyonu belirlenerek ve ardından dofset maksimum büzülme varyasyonuna eşit ayarlanarak yüzey ofseti takım değiştirmesi belirlenir.
Daha önce tartışılan termal işlemlere ek olarak, metal veya seramik parçalar üretmek için AM’yi fırın işlemeyle birleştirmek için yıllar içinde bir dizi başka prosedür geliştirilmiştir. Örnek bir yaklaşım, gaz geçirmeyen kaplamalara sahip gözenekli parçalar üretmek için lazer sinterlemeyi kullandı.
SLS ile imalat sırasında bir parçanın yalnızca dış konturlarını tarayarak, gevşek tozla doldurulmuş bir metal “kutu” yapılır. Bu parçalar daha sonra sıcak izostatik presleme (HIP) kullanılarak tam yoğunluğa kadar sonradan işlenir. Bu yerinde kapsülleme, hiçbir olumsuz kap-toz etkileşimi (aynı toz yatağından yapıldıkları için), azaltılmış ön işleme süresi ve konserve parçaların geleneksel HIP’sine kıyasla daha az işlem sonrası adımı ile sonuçlanır.
SLS/HIP yaklaşımı, havacılık uygulamaları için Inconel 625 ve Ti–6Al–4 V’de karmaşık 3D parçalar üretmek için başarıyla kullanıldı. Karmaşık şekilli ZrB2/Cu kompozit EDM elektrotları üretmek için lazer sinterleme de kullanılmıştır.
Yaklaşım, (a) lazer sinterleme kullanılarak polimer kaplı ZrB2 tozundan yeşil bir parçanın üretilmesini, (b) ZrB2’nin ayrıştırılması ve sinterlenmesini ve (c) sinterlenmiş, gözenekli ZrB2’nin sıvı bakır ile sızmasını içeriyordu. Bu üretim yolunun, sıcak presleme yoluna kıyasla daha homojen bir yapı sağladığı görülmüştür.
AM tarafından üretilen parçaların çoğu, amaçlanan kullanımlarında uygulanmadan önce son işlem gerektirir. AM süreçlerinin etkili bir şekilde kullanılması, yalnızca AM sürecinin faydaları ve sınırlamaları hakkında bilgi sahibi olmayı değil, aynı zamanda kullanım için parçayı sonlandırmak için gerekli olan gerekli son işleme operasyonlarını da gerektirir.
AM tarafından üretilen bir parça için amaçlanan form, uyum ve işlev göz önünde bulundurulduğunda, tipik olarak sonradan işleme gerekir. Doğru formu elde etmek için, destek malzemesinin çıkarılması, yüzey dokusu iyileştirmeleri ve estetik iyileştirmeler genellikle gereklidir.
Doğru uyumu elde etmek için, genellikle frezeleme yoluyla doğruluk iyileştirmeleri gerekir. Doğru işlevi elde etmek için AM parçası, model olarak kullanım için hazırlık, termal olmayan teknikler kullanılarak özellik geliştirmeleri veya termal teknikler kullanılarak özellik geliştirmeleri gerektirebilir.
İster otomatik ikincil destek malzemesi çıkarma, emek yoğun dekübasyon, yüksek sıcaklıkta fırın işleme veya ikincil işleme kullanıyor olun, amaçlanan uygulama için en iyi AM sürecini, malzemeyi ve son işleme kombinasyonunu seçmek ve uygun şekilde uygulamak, başarı için kritik öneme sahiptir.
IDE açılımı Ide Nedir İde nedir programlama IDE örnekleri ne ise yarar tümleşik geliştirme ortamları (ide) amaçları What is IDE Yazılım geliştirme Ortamı Nedir
Son yorumlar